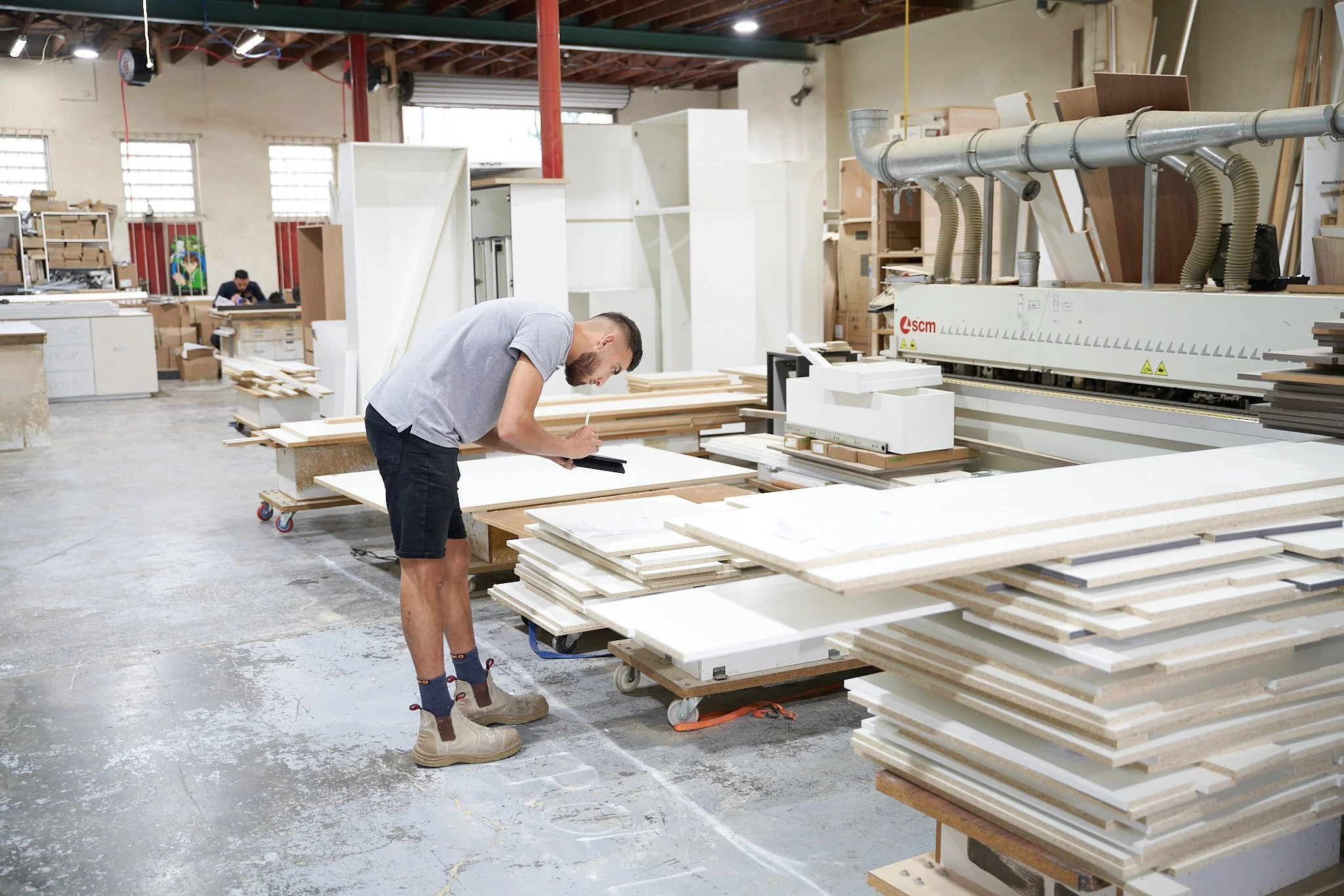
Quality Control
At Exquisite Kitchens, quality is at the core of our operations, ensuring that every project we undertake regardless of size or sector meets the highest standards. Our commitment to excellence begins with meticulous planning, where we engage in comprehensive consultations with builders and developers to understand their unique requirements. This initial phase allows us to align our design and production processes, ensuring that each kitchen is tailored to the specific needs of the project, whether it’s a high-rise apartment complex or a childcare centre.
Our quality control procedures are robust and systematic, encompassing every stage of the kitchen remodelling process. From selecting premium materials to employing skilled craftsmen, we maintain rigorous standards that are consistently monitored. Throughout fabrication, we conduct multiple quality checks to ensure that each component meets our exacting specifications. This diligence extends to the installation phase, where our experienced team meticulously fits each kitchen, ensuring that they not only function seamlessly but also exude aesthetic appeal.
Moreover, Exquisite Kitchens values feedback as a key component of our quality assurance strategy. Following project completion, we perform thorough evaluations to assess client satisfaction and pinpoint any areas for improvement. This iterative process fosters an environment of continuous enhancement, enabling us to refine our practices and deliver even higher quality in future projects. By adhering to these comprehensive quality control measures, we confidently cater to diverse sectors and project sizes, consistently exceeding expectations.
Stage 1:
Planning a kitchen install involves a meticulous approach to ensure a seamless execution that meets both functional and aesthetic requirements. First, it’s essential to assess the space available, considering factors like layout, flow, and natural light. Engaging with designers to create detailed plans will help in selecting materials and finishes that align with the project’s budget and style. Coordination with builders is crucial for aligning timelines and ensuring that plumbing, electrical, and structural considerations are addressed prior to installation. Proper scheduling and communication with all stakeholders will contribute to a smooth process, minimising disruptions and ensuring the project is completed on time.
Stage 2:
Designing a kitchen for a residential project and a unit complex requires a keen understanding of both functionality and aesthetics to accommodate a diverse range of lifestyles. In residential settings, the focus is often on creating a warm, inviting space that maximises storage, encourages family interactions, and reflects the homeowner's personal style. In contrast, kitchens for unit complexes must prioritise efficiency and durability, ensuring that the design can withstand high usage while remaining attractive to potential tenants or buyers. This entails incorporating sleek, modern appliances, utilising space-saving cabinetry, and selecting finishes that are not only stylish but also easy to maintain. Ultimately, both projects should balance visual appeal with practicality, ensuring that each kitchen serves its purpose while enhancing the overall value of the property.
Stage 3:
Manufacturing kitchen panels in volume requires precision engineering and a robust supply chain to meet the demands of large-scale projects. This process involves sourcing high-quality materials that ensure durability and aesthetic appeal, followed by advanced cutting and finishing techniques that adhere to industry standards. By utilising state-of-the-art machinery and streamlined production methods, manufacturers can efficiently produce large quantities of panels with consistent quality and design. Additionally, maintaining effective communication with builders and developers is crucial to align production schedules with project timelines, ultimately delivering outstanding results for large residential and commercial developments.
Stage 4:
Quality Control.
Quality control is a critical component in the kitchen remodelling process, ensuring that each project meets the highest standards of craftsmanship and durability. At Exquisite Kitchens, we implement rigorous quality control measures throughout every phase, from initial design to final installations. Our team conducts thorough inspections and detailed assessments, verifying that materials and workmanship align with industry benchmarks and client specifications. By maintaining stringent quality control, we not only enhance the aesthetic appeal of our kitchens but also guarantee their functionality and longevity, ultimately ensuring complete client satisfaction.
Stage 5:
Logistics.
The efficient delivery of panels to the job site is crucial for maintaining the momentum of the project. Each panel is carefully loaded onto the truck, ensuring that they are secured to prevent any damage during transit. Timely arrival is essential, as it allows the construction team to proceed with their schedules without delay. Upon arrival, the panels are unloaded with precision, following safety protocols to protect both the materials and the workers on site. This streamlined process not only upholds the quality of our services but also reinforces our commitment to meeting the demands of builders and developers in delivering exquisite kitchens on time.
Stage 6:
Installation.
The installation of the kitchen is a crucial phase in the remodelling process, requiring precision and expertise to ensure a seamless integration of design and functionality. Skilled tradespeople systematically lay out the cabinetry, ensuring each unit is level and aligned for optimal performance and aesthetic appeal. Plumbing and electrical fixtures are installed concurrently, adhering to local codes to guarantee safety and efficiency. The careful placement of countertops and appliances follows, with a focus on ergonomic design to enhance workflow. Meticulous attention to detail is vital, as it sets the foundation for a beautiful and efficient kitchen that will meet the demands of everyday use.
Stage 7:
Final assessment.
Assessing a kitchen after installation is a critical step in ensuring the quality and functionality of the space. It involves a thorough inspection of all components, including cabinetry, countertops, appliances, and plumbing fixtures, to confirm that they meet the specified standards and design intentions. During this assessment, attention should be paid to the alignment of cabinets, the evenness of countertops, and the proper functioning of appliances. Additionally, checking for any imperfections, such as scratches or dents, is essential for maintaining a high-quality finish. Addressing any issues promptly not only enhances the aesthetic appeal but also ensures long-term satisfaction for clients, contributing to the overall success of the project.